
Opportunity
The primary problem in the field of soldering technology, particularly for 3D integrated circuits (3D ICs), is the reliance on high-temperature soldering processes, which are unsuitable for modern microelectronic applications. Traditional solder alloys require temperatures above 200°C, which can damage sensitive components and limit manufacturing efficiency. Challenges must also be addressed to make reliable solder joints in micron ranges. Existing methods of producing small solder particles often result in non-uniform sizes and shapes, reducing solder joint reliability. Another challenge concerns the need to control the shape of the liquid solder. Although ultrasonic vibration has been developed to prepare small and uniform solder particles, there is insufficient research on the practical applications of multi-alloy solder particles, which restricts innovation in solder materials. There is thus a need for an improved solder material and method that facilitate bonding at lower temperatures and enable the creation of solder joints in micron ranges.
Technology
The technology involves a new type of solder made from a mixture of three metals, namely tin (Sn), bismuth (Bi), and indium (In), and a method of producing the Sn–Bi–In base solder particles. This method is based on the discovery that solder paste with micron-size particles can be produced by subjecting an alloy to ultrasonication under suitable conditions. A solder alloy comprising Sn–Bi–In particles each less than 10 µm in diameter is produced by (a) sintering a mixture of Sn, Bi and In to produce a bulk alloy with a melting point of about 60–65°C; (b) dissolving the bulk alloy in an ethylene glycol solution to produce an alloy solution; (c) ultrasonicating the alloy solution at about 65–85°C for 10 to 150 minutes to produce a suspension; and (d) cooling the suspension to about 0–25°C to produce the base solder particles.
Advantages
- The new Sn–Bi–In base solder can bond at significantly lower temperatures (around 60°C), which reduces the risk of damaging sensitive electronic components during the soldering process. This is particularly beneficial for modern electronics that require careful handling.
- The use of very small solder particles (less than 10 micrometers in diameter) enhances the bonding between substrates and solder particles. Smaller particles can fill gaps more effectively, leading to stronger and more reliable connections.
- The method of producing solder particles through ultrasonication ensures that the particles are uniform in size. This uniformity is crucial for achieving consistent solder joints, which can improve the overall performance and reliability of electronic devices.
- The technology allows for the creation of solder joints that can withstand the stresses and strains of modern electronic applications. The improved mechanical properties of the solder can lead to better performance in devices, especially in applications where reliability is critical.
Applications
- Consumer electronics manufacturing
- The automotive industry
- Production of advanced semiconductor devices and 3D integrated circuits
- Soldering of delicate components, e.g., in medical devices.

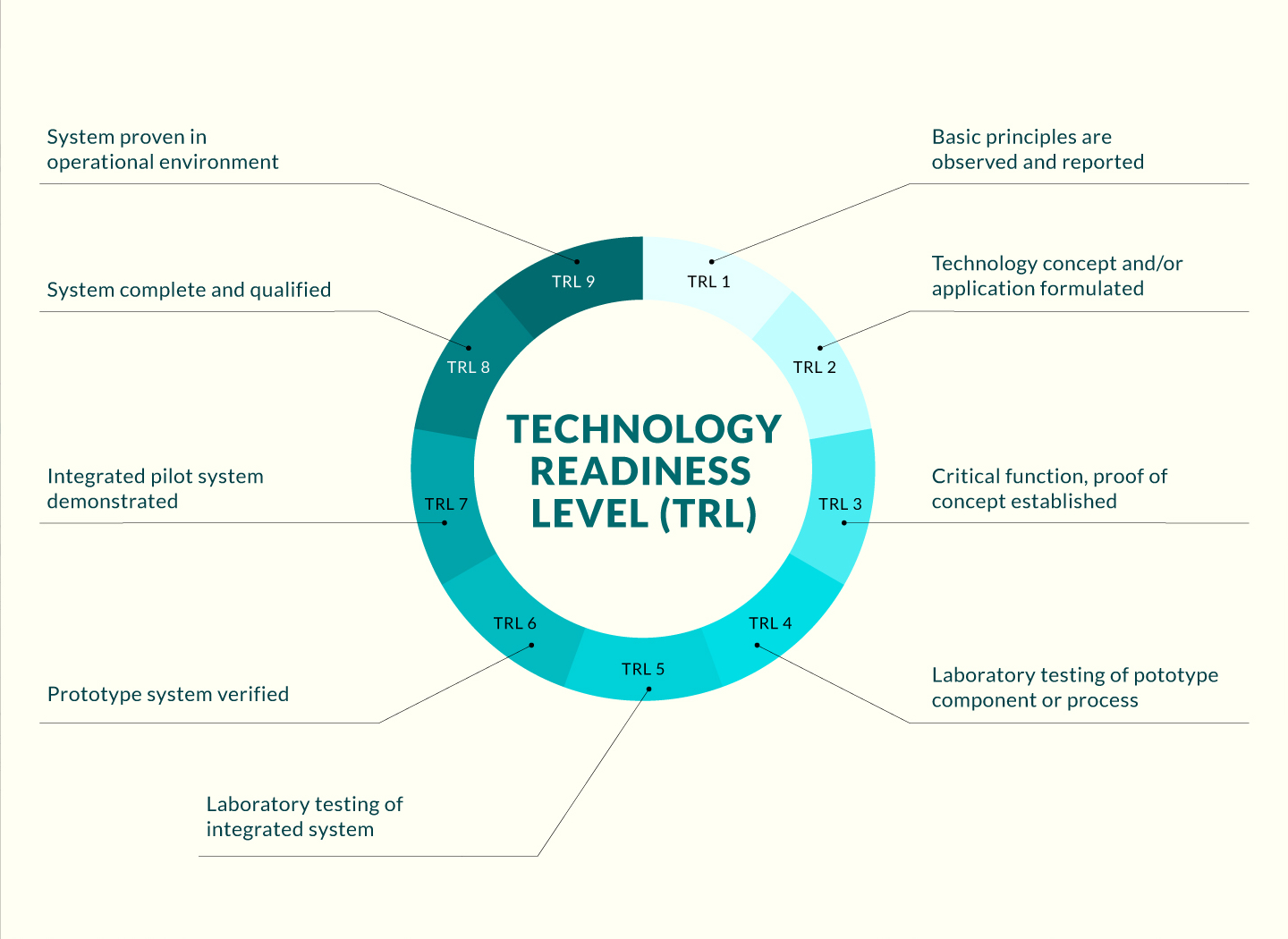
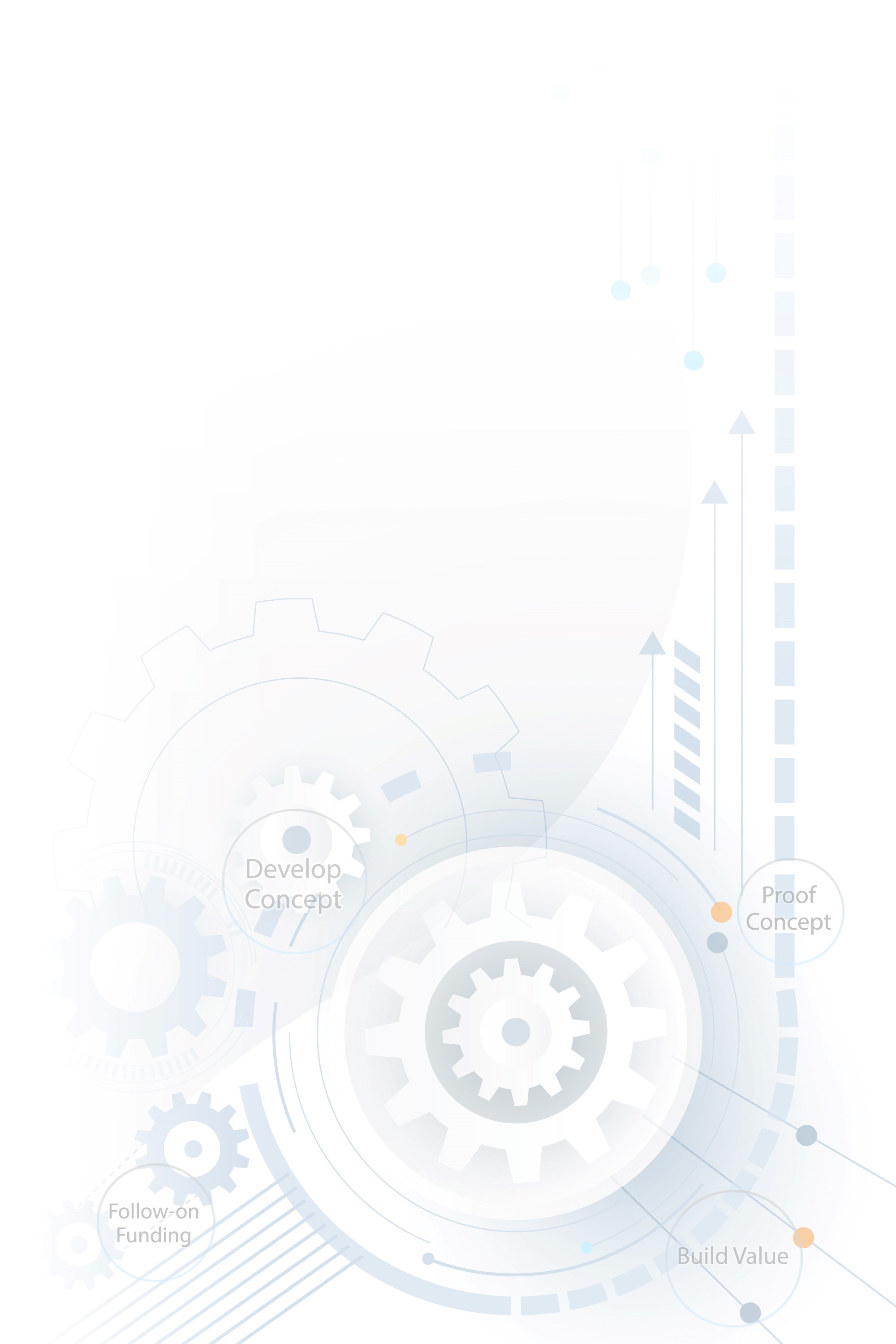