
Opportunity
Engineering progress is underpinned by improvements in the properties of steel. Steels have been strengthened considerably in recent decades through the development of nanocrystalline alloys, which have grain sizes refined to the nanoscale. However, strength improvements come at the cost of reduced ductility, which limits the workability and applications of ultra-strong steels. The existing strategy to minimise the strength–ductility trade-off is nanotwin strengthening. However, nanotwinned metals are still much less ductile than traditional coarse-grained metals. To improve ductility while retaining ultra-high strength, the key is to modify the alloys’ plastic deformation mechanism. Plastic deformation of conventional nanotwinned alloys relies on interactions between dislocations and twin boundaries. To finally resolve the strength–ductility trade-off, nanotwinned steels with a novel deformation mechanism that involves strain delocalisation must be developed.
Technology
The technology is a steel alloy that avoids the strength–ductility trade-off. The steel has a dynamically transformable nanotwinned (DT-NT) structure, in which the austenite phase of steel partly converts to the martensite phase when under strain. This transformation increases the strain-hardening capability of the steel, improving its strength and ductility simultaneously. The dynamically transformable nanotwins are created in the austenite phase, after quenching of the steel, during the forming process. The nanotwin boundaries impede dislocations and promote the formation of martensite under strain, which suppresses strain localisation and improves ductility through transformation-induced plasticity. The DT-NT steel thus achieves an ultra-high strength on the order of gigapascals while remaining as ductile as commercial austenite steels. It is produced by conventional processes and can be made on a large scale at low cost, with the potential to replace austenite steels in the automobile, construction, and aerospace industries.
Advantages
- Retains unprecedented ductility when yield strength is increased to 1–2 GPa – its uniform elongation is one order of magnitude greater than that of other steels with similar hardness
- Safer, cheaper, and more processible than 304 and 316L stainless steels
- Stronger than dual-phase steels, martensite steels, and high-manganese steels
Applications
- Highly formable and can be manufactured in complex shapes for industrial purposes
- Potential replacement for austenite steels in cars, aeroplanes, and buildings where excellent strength and ductility must be combined

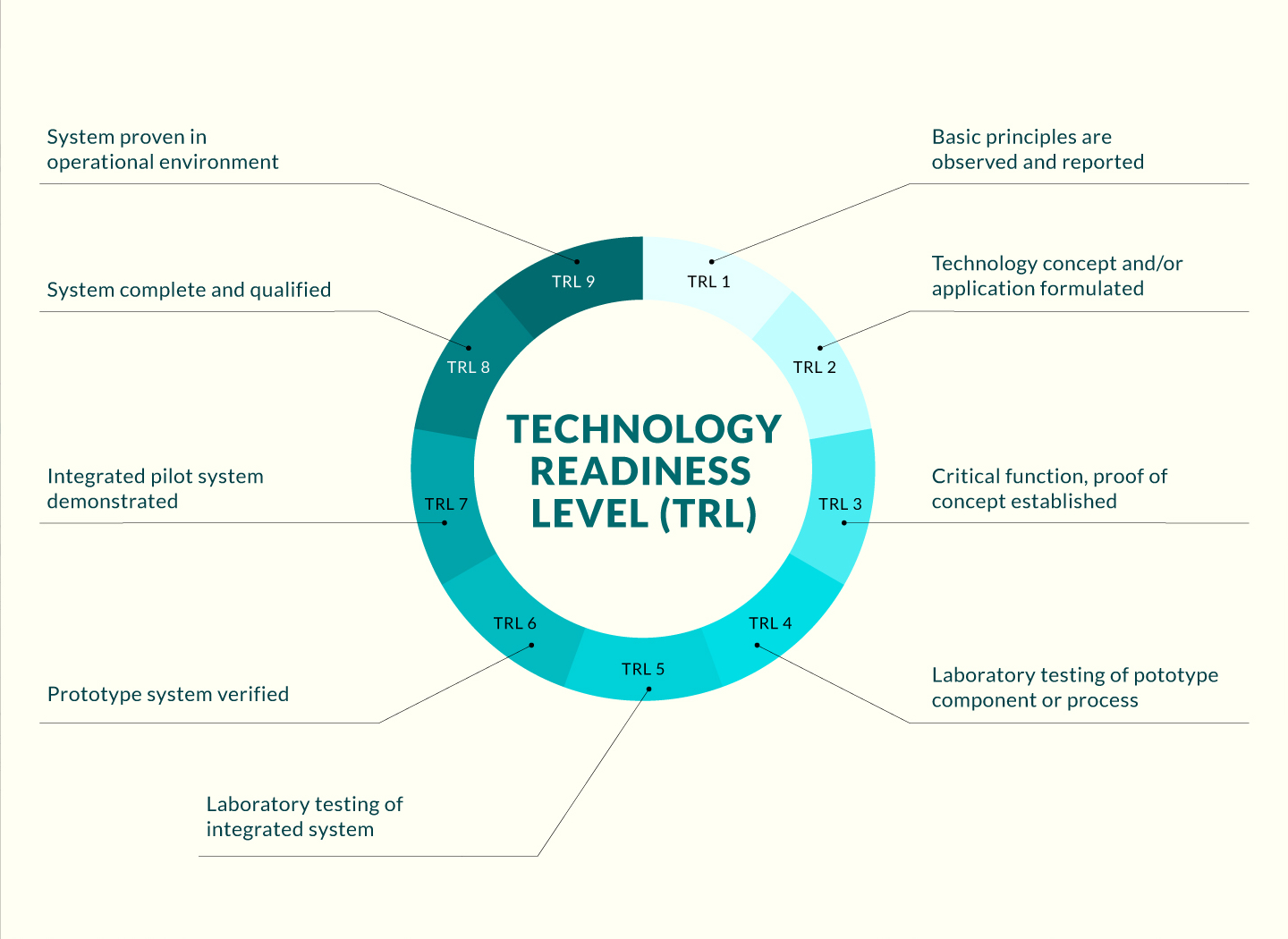
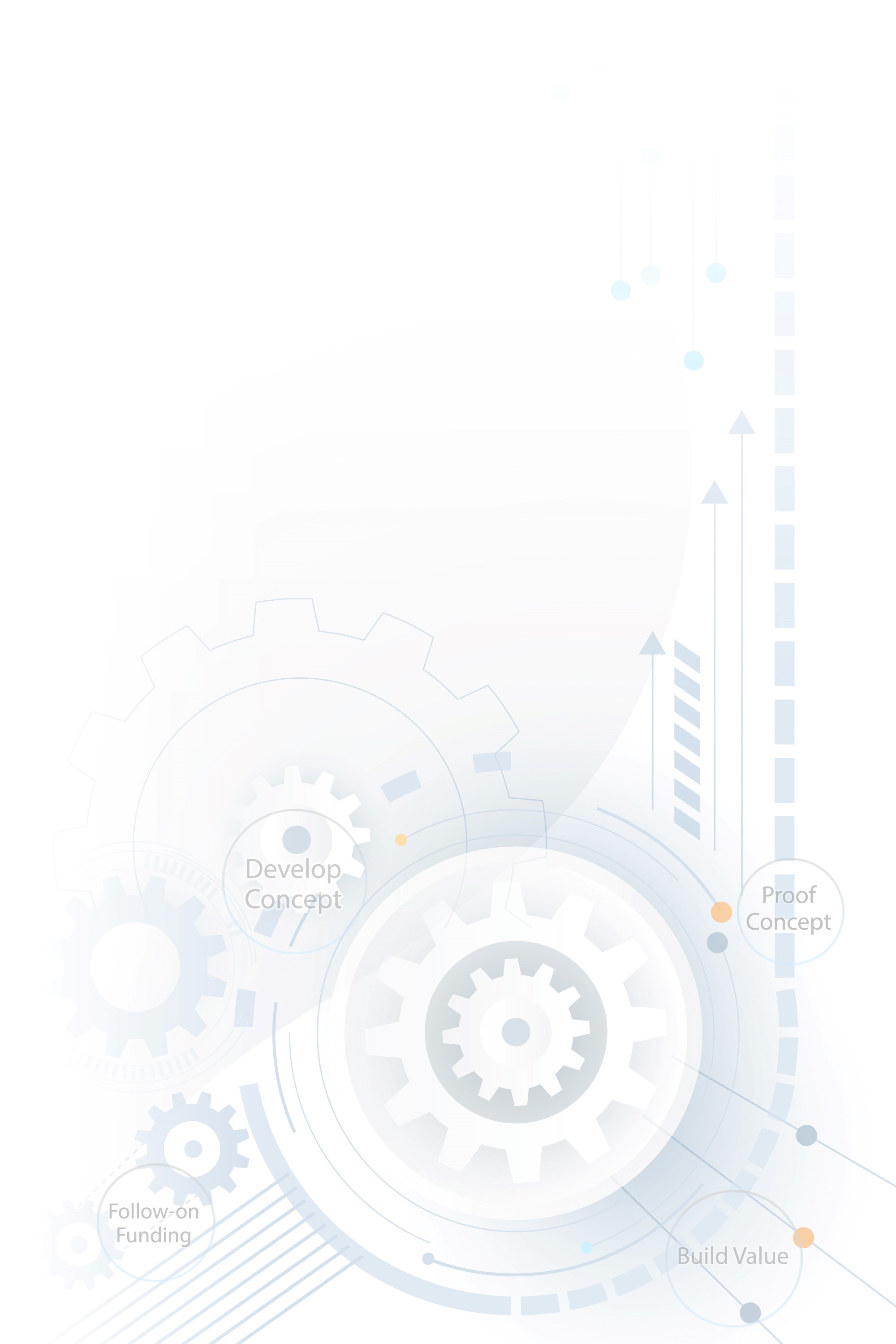