
Opportunity
One-dimensional (1D) micro/nanomaterials, such as micro/nanowires and nanotubes, sparked a wide range of investigations due to their unique physical properties and functional applications. Compared to their bulk counterparts, low dimensionality and high surface-to-volume ratios of them result in wide difference in terms of the optical, electrical, thermal, and mechanical behaviours. However, characterization of these properties at such small scales remains extremely challenging but critical for their practical applications such as stretchable electronics.
Technology
The present invention relates to a method of constructing a micromechanical device by additive manufacturing for characterizing strength of a low dimensional micromaterial or nanomaterial sample. The method includes: a) deriving a three-dimensional representation arranged to represent a said micromechanical device with reference to at least one physical characteristic of a said low dimensional material sample; b) transforming the three-dimensional representation into a plurality of two-dimensional representations arranged to individually represent a portion of the three-dimensional representation; and c) forming the micromechanical device from a fluid medium arranged to transform its physical state by stereolithography apparatus in response to a manipulated illumination exposed thereto, whereby a said low dimensional material sample is loaded onto the formed micromechanical device.
Advantages
- Much facile to control the complex and arbitrary shape of a micromechanical device
- Low-cost and less time consuming in comparison with the method of photolithography process
- More flexible on the choice of photopolymer and topological design for different samples
Applications
- Micro-electromechanical system (MEMS) type device and Micro-mechanical device (MMD)
- In situ tensile testing of micro/nanowires

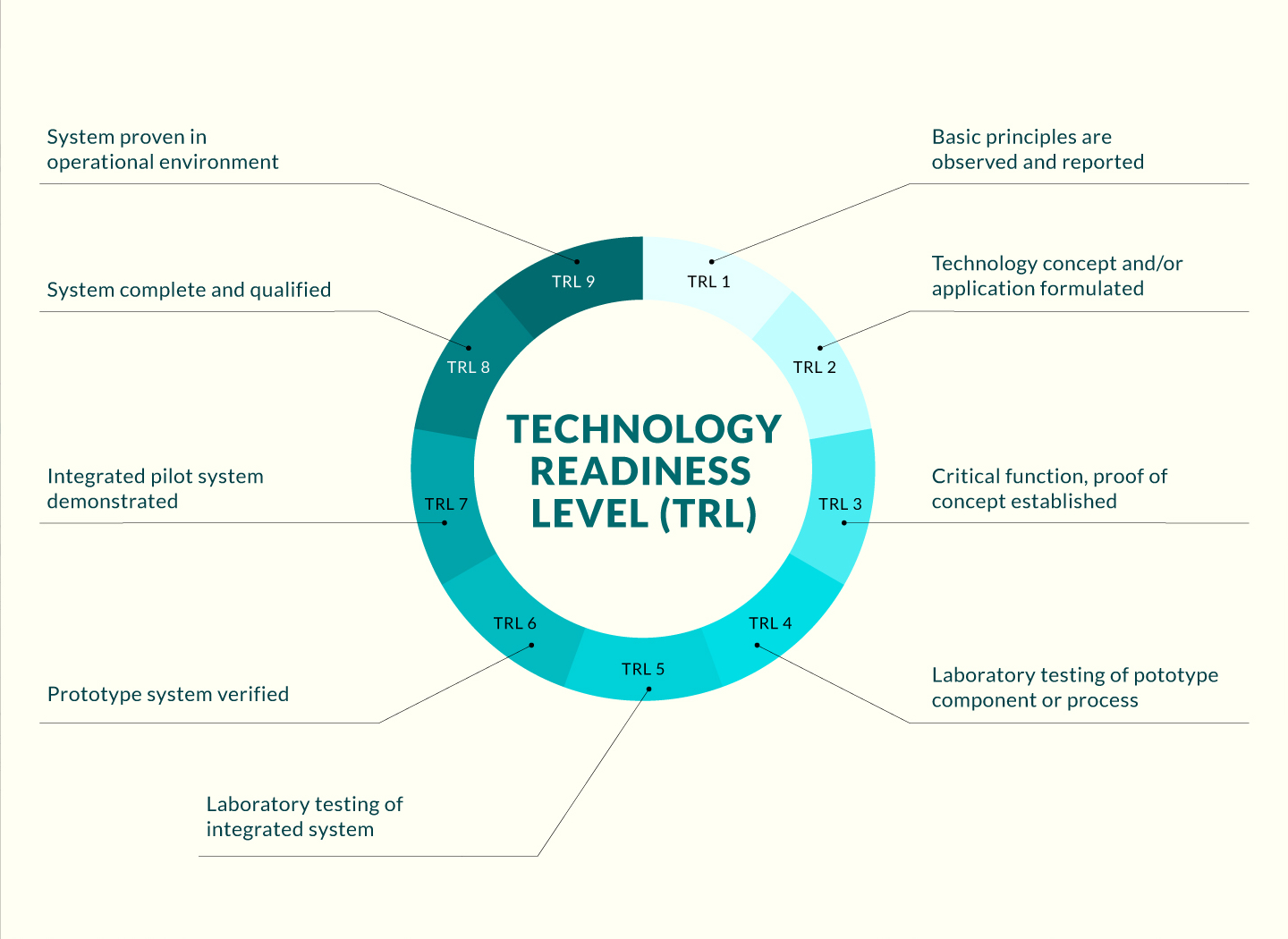
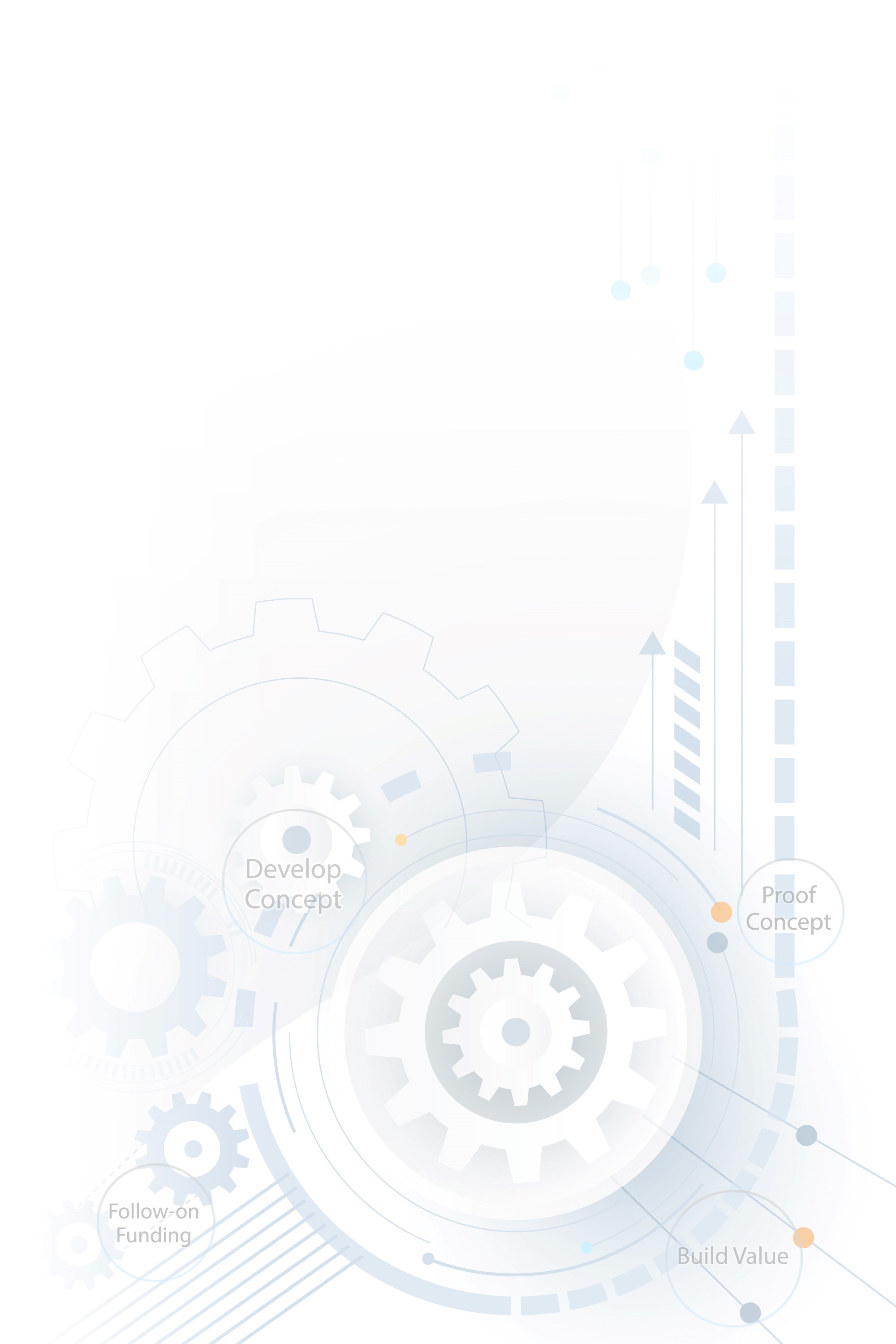