


Opportunity
The present invention is a human-machine interface (HMI) system that provides 7 sensing channels and 5 actuating channels for robotics feedback. The self-developed bending sensors are mounted onto human joints to accurately capture human motions, including knuckles, wrists, elbows, shoulders, leg-ends, knees, ankles, etc. The bending sensors support a wide detection angle range with high sensitivity, fully covering the human motion requirements. The bending sensor also serves as a pressure sensor mounted on robotics to acquire feedback information. The self-developed vibratory actuators based on electromagnet effects are attached to the target area of the body. The vibration amplitude of the actuator can increase according to the feedback information from the pressure sensor of the robotics to create a real sense for the user. Due to the advanced mechanical design, the control module can still work as normal under various mechanical deformations, including stretching, twisting, and bending. By introducing Bluetooth technology, the control and feedback can be done wirelessly.
Technology
The new generation of the human machine interface (HMI) system provides 7 sensing channels and 5 actuating channels for robotics feedback. To capture the human motions accurately, the self-developed bending sensors (30 mm×10 mm×1.8 mm) are mounted onto human joints, including knuckle, wrist, elbow, shoulder, leg end, knee, ankle, e.g. The bending sensors support a wide detection angle range from 0 to 90° with a high sensitivity of 0.0274 /°, fully covering the human requirement. Due to the excellent electrical performance, the bending sensor also serves as a pressure sensor mounted onto robotics for the purpose of feedback information. To create a real sense on user, the self-developed vibratory actuators (diameter, 7 mm; thickness, 1.9 mm) based on electromagnet effect are attached onto the target area of human body by adhesive tape. The vibration amplitude by the actuator can increase from 0 to 0.3 mm with the increasing frequency from 0 to 250 Hz. Therefore, users can sense different pressure by adjusting the vibration frequency of the actuators. Both the bending sensors and actuators are directly connected to the flexible central control module by wire. Owing to the advanced mechanical design, the control module (70 mm×50 mm×2 mm) can still work as normal under various mechanical deformations, including stretching, twisting, and bending. Please find the more information of the HMI system in the attached file.
Advantages
- Remote controlling various complicated robotics
- Withstand various mechanical deformations, including stretching, twisting, and bending
- Low wireless transmission latency
Applications
- The new HMI system enable users to remotely manipulate various robotics, including but not limited to driverless vehicles, complicated robots.
- The HMI system can help disable people to obtain more job opportunities. For example, a user with hand disability can remotely manipulate a robot to carry heavy goods by equipping the HMI system.
- By wearing the HMI system, doctors can remotely control a robot to operate a delicate surgery.
- By wearing the HMI system, the medical workers can remotely manipulate the robots to look after the infected people, greatly decreasing the infected risk.
- The HMI system can help to decrease the life risk of soldiers as they conduct the dangerous work remotely.

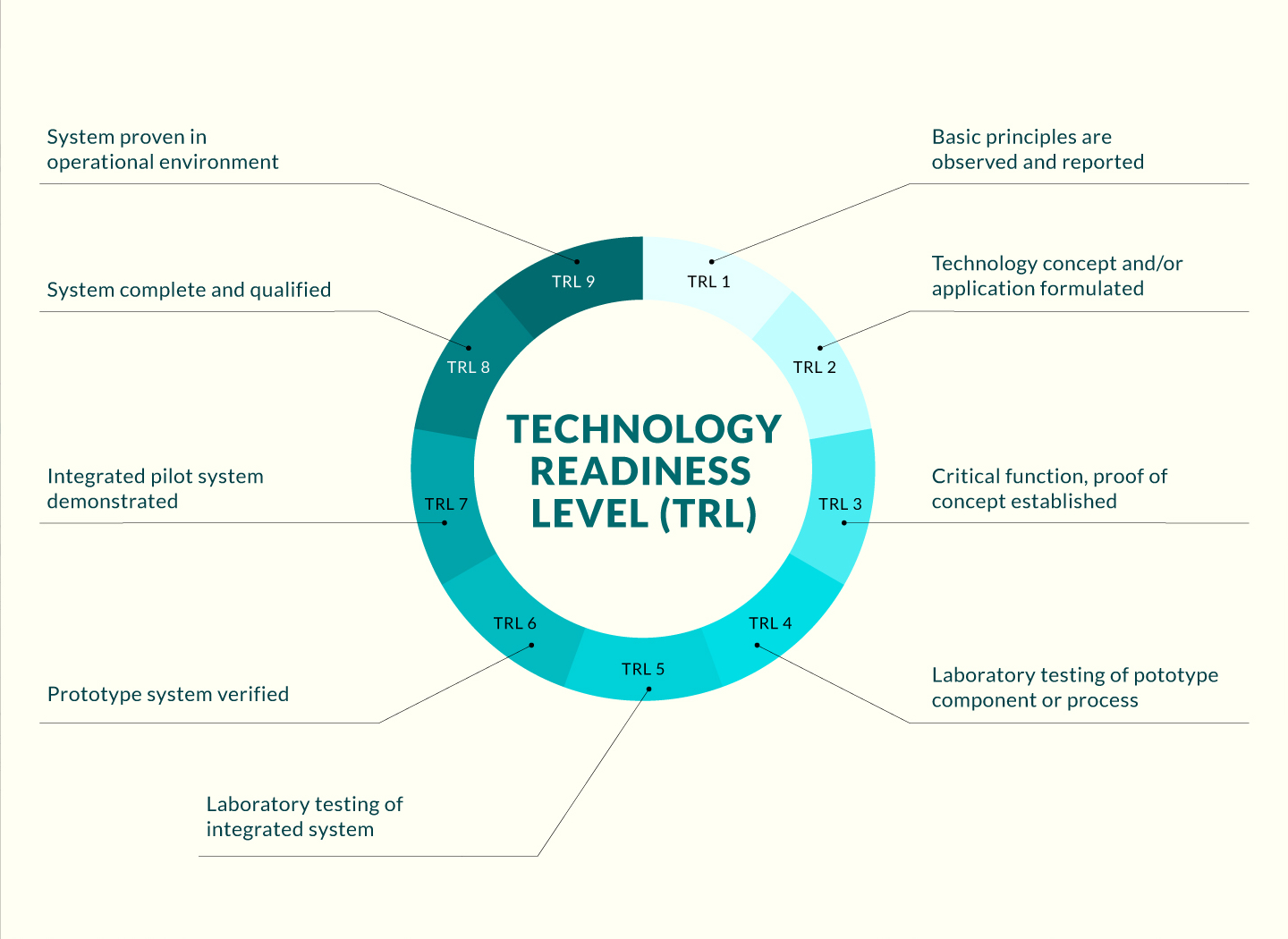
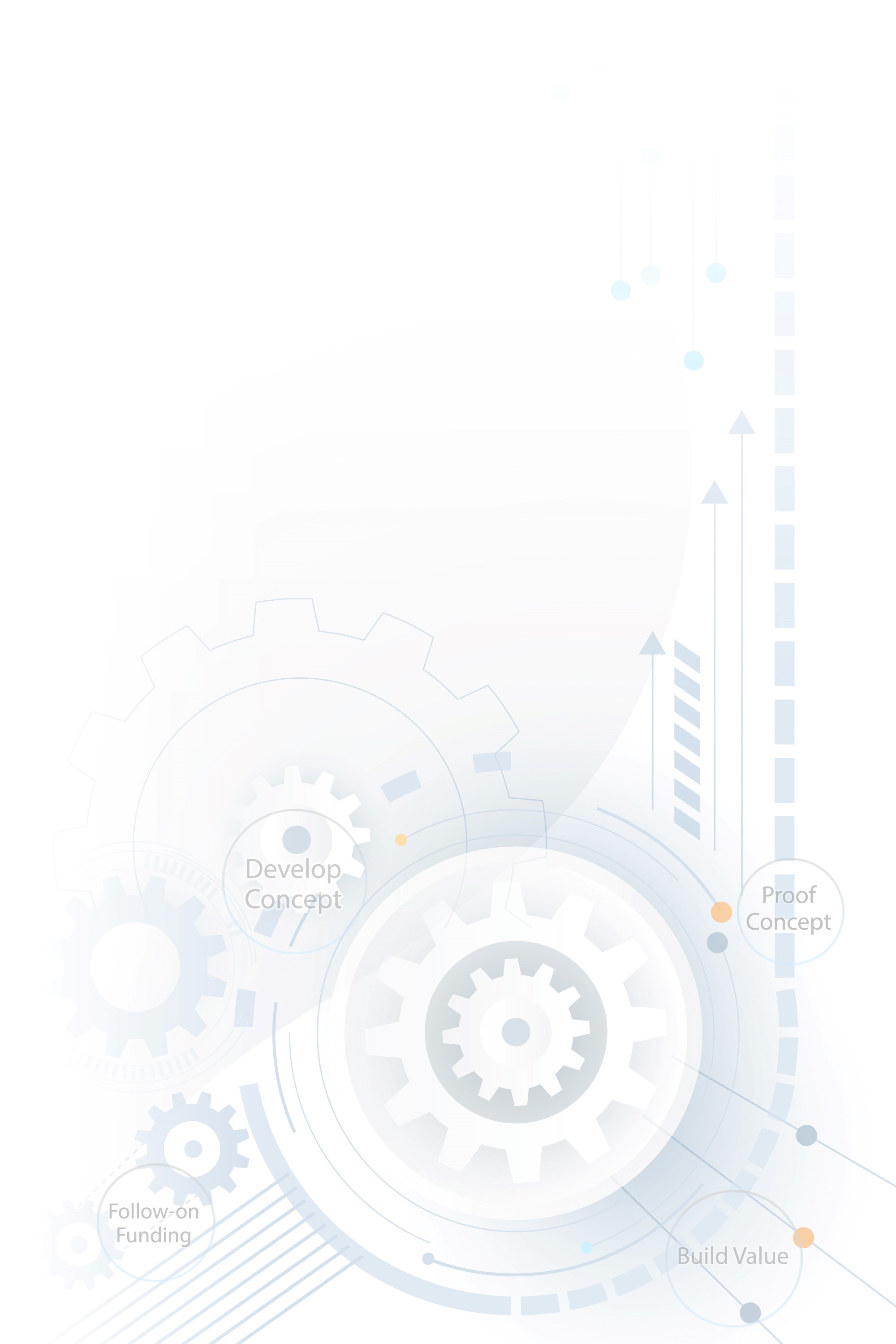